Printed circuit boards come in all different shapes and sizes. Some can be huge, while others can be tiny – about the size of a quarter. With all the varying sizes and designs of PCBs, there lies the challenge of assembling them for our partners.
Boards can have critical components that are located on the front, the back, and even through the board itself. For employees who hand solder, challenges can arise when components are located on both sides of the boards. For example, they can’t put too much pressure on the boards while they are soldering parts or they risk breaking some of the components on the opposite side. As a company that is steadily growing and getting more work as time progresses, the company doesn’t have the time to repair or re-print new boards for every part that breaks.
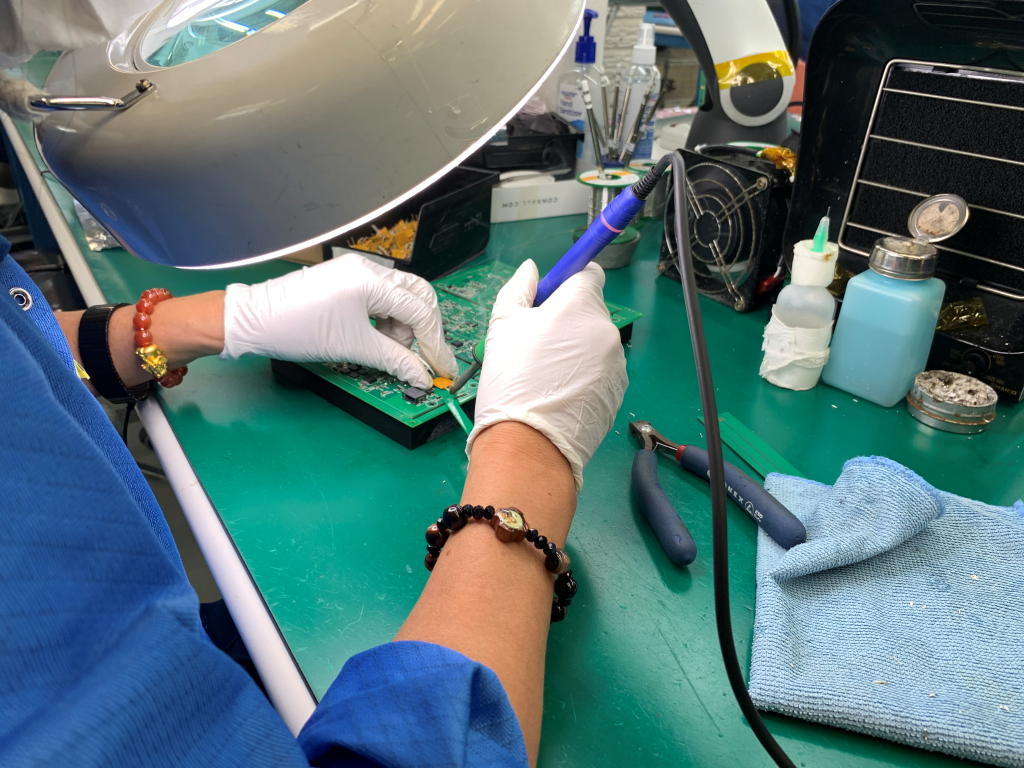
NCA practices lean manufacturing and fixes issues at the root of the problem. The company is proactive rather than reactive, so NCA’s process engineers tackled this obstacle and found the solution. Using additive manufacturing tools and technology, Ram Gudavalli, an NCA process engineer, was able to create a fixture to ensure the safety of critical components during the hand soldering process. This fixture fits the panels and allows our team members to hand solder without the concern of pressing too hard on the board and breaking components on the opposite side. As seen in the images above, the panel is placed on the printed “stand”, which elevates the panel above the table and protects the bottom side of the boards.
Searching for and finding the bottlenecks of assembly processes and providing long term solutions keep NCA adaptable to the changing environment while eliminating lean manufacturing waste.
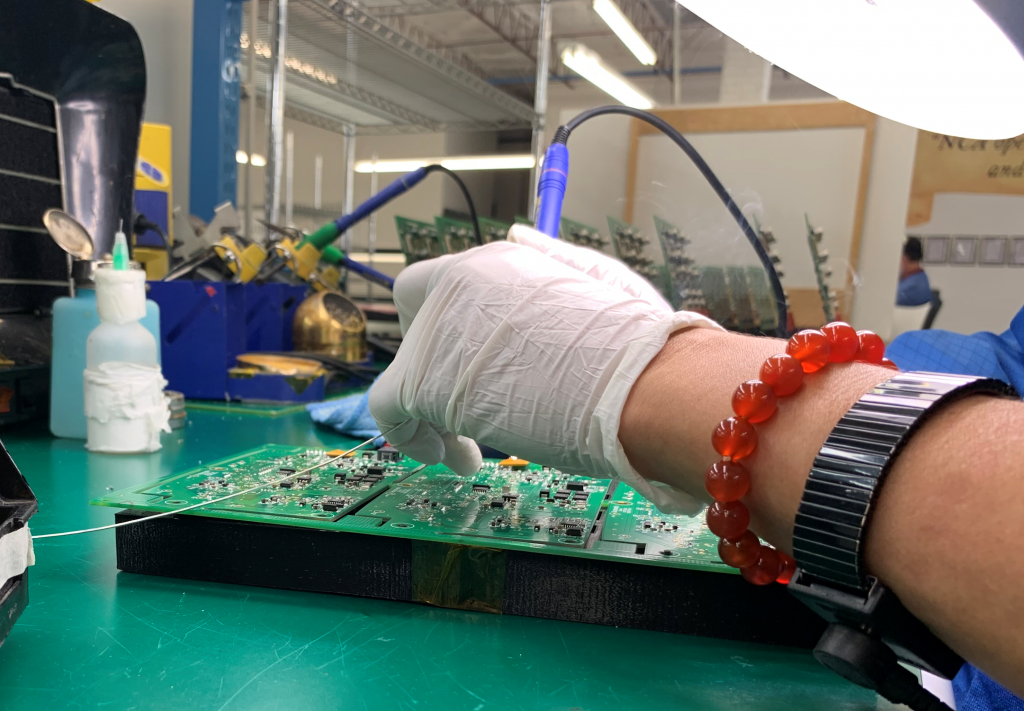